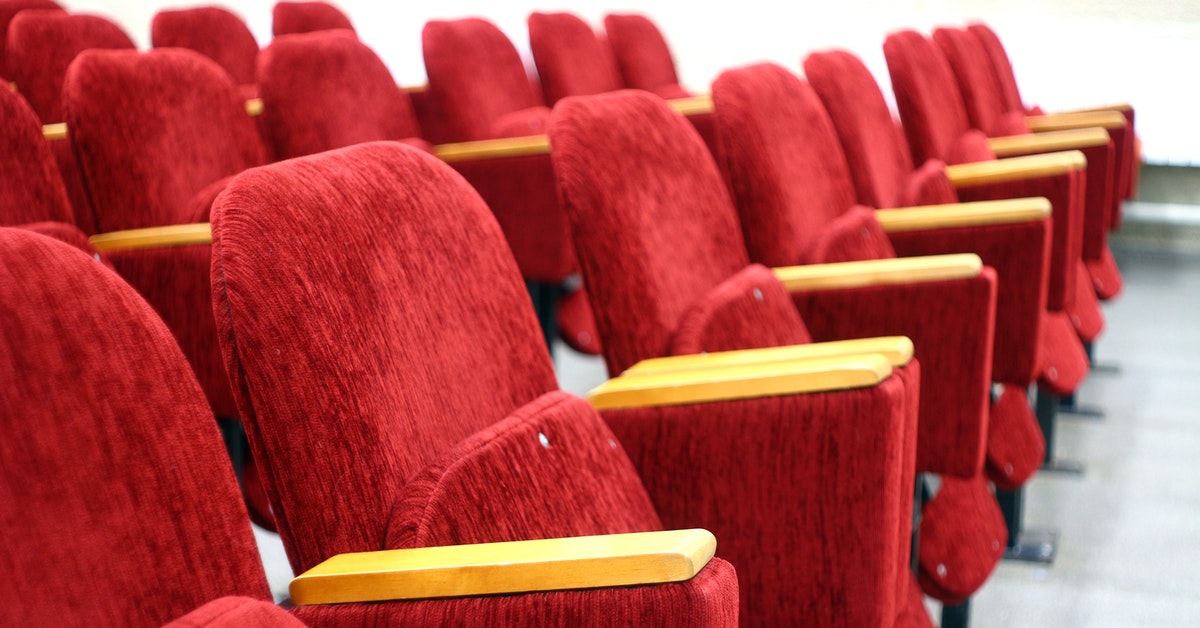
Hidden value of mustering drill and the importance of practice.
“Good teams perform better in games than they do in practice, but great teams practice great.” That’s a quote an early mentor said to me while explaining how we would approach Safety. It’s stayed with me ever since and I’ve applied it to many aspects of my professional and personal life.
I took it to mean that many people are “gamers”; people who will step up and exceed even their own expectations when the chips are down. But I also took it to mean that those people are rare. Teams are usually made up of one or two “gamers.” The remainder are mere mortals who must train extra hard to triumph in competition. In other words, a team will perform to the level of its preparation.
Preparation can only be achieved through practice, especially preparing for the unexpected. This is a core principle in our mission to improve emergency response for chemical plants and refineries. The vast majority of facilities run fewer than 4 mustering drills per year. This means that there are people who’ve worked at the site for months and never practiced a mustering drill. In some cases, this could be hundreds of people. Far worse than mediocre practice, that’s no practice at all! This leaves the site vulnerable to failure when an emergency occurs.
Since the introduction of AllClear, we’ve espoused the importance of following a path of Continuous Improvement by conducting frequent drills. Drills are the backbone of Continuous Improvement because they:
- Generate data that can illuminate vulnerabilities in the mustering process. Examples include non-compliance, bottlenecks, and communication gaps.
- Measure improvement from drill to drill to confirm that process changes are maintained and benefits persist.
- Build muscle memory among the plant staff through repetition and enable them to “practice great”.
Many facilities choose to drill infrequently because they believe that productivity interruptions should be minimized. The common assumption is that drills consume so much time that, taking into account important productivity metrics, the appropriate frequency for drills is once per quarter or less. This perpetuates the conventional belief that the plant is prepared, despite evidence to the contrary.
That’s why “Best In Class” facilities develop processes that minimize productivity disruption. This allows them to run drills more frequently. They’ve concluded (some from research and some from painful lessons learned) that this effort is worth the cost. It makes the site more ready with each drill. Aside from the promise to send staff home safely each day, a few draw on the research that a fatality will cost the site upwards of $9M. In the end, the productivity impact of each drill is reduced while the frequency of the drills is increased.
AllClear users drill more frequently
We built AllClear with the help of emergency responders and safety managers to equip them with the tools to “practice great”. The system turbocharges mustering data collection and visualization. It also adapts to each site’s unique mustering process. This empowers AllClear users to embark on a data-driven path of continuous improvement by measuring drills, analyzing the data, implementing improvements, and doing it all over again and again.